Our 4-in-1 Laser Welding Machine, as its name implies,perfectly integrates four functions: laser cleaning, cutting, welding, and laser weld seam cleaning. In traditional industries, different processes often require switching between different devices. This not only increases equipment costs but also prolongs the production cycle and reduces work efficiency. However, the emergence of our 4-in-1 Laser Welding Machine has completely changed this situation.
In the current context where green environmental protection is advocated globally, our 4-in-1 Laser Welding Machine stands out with its high – efficiency and energy – saving characteristics. The laser technology itself has the advantage of high – energy conversion efficiency. Compared with traditional methods such as mechanical processing and chemical cleaning, laser equipment consumes less energy during operation and can achieve precise energy output, avoiding unnecessary energy waste.
No chemical reagents are required during the cleaning process, which reduces water resource pollution and chemical hazards to the environment. Meanwhile, the smoke and harmful gases generated during laser cutting and welding are relatively few. In addition, the equipment is equipped with an efficient smoke purification system that can timely filter and purify the generated smoke to ensure the air quality of the working environment and provide a healthy and safe working environment for operators.
Regarding the laser aspect, the 4-in-1 Laser Welding Machine can easily remove rust, chemical traces, stains, damage, etc. from the surface of various materials. Its cleaning principle is to use a high – energy laser beam to irradiate the material surface, causing the substrate to heat up and expand rapidly, and peel off the substrate instantaneously without any damage to the substrate. The entire process does not require any reagents for cleaning.
The cutting function of the 4-in-1 Laser Welding Machine realizes powerful energy and precision control capabilities. Whether it is metal sheets, pipes, or other hard materials, they can be accurately separated by laser cutting. The cutting edges are polished and then undergo subsequent processing, which greatly improves the processing quality and efficiency. Moreover, the laser cutting accuracy can meet the cutting requirements of various complex shapes and sizes, providing great convenience for the processing of parts in industrial manufacturing.
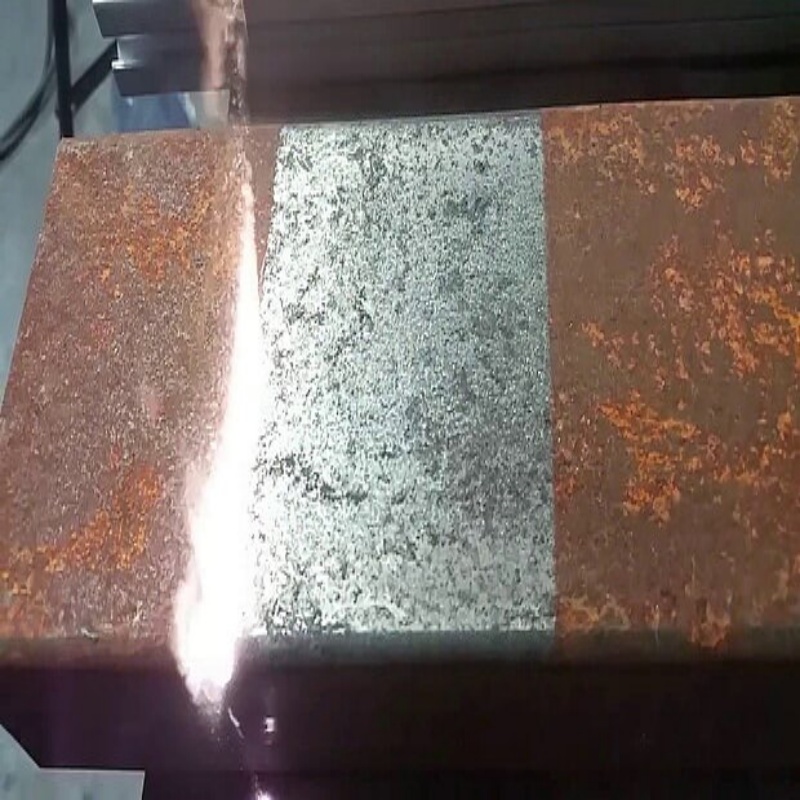
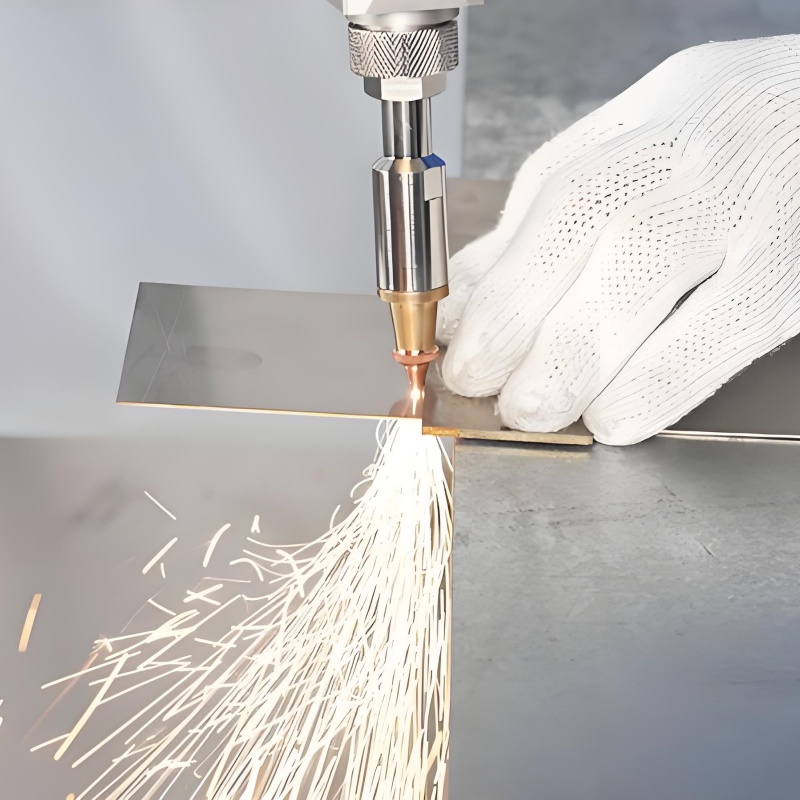
The welding function of the 4-in-1 Laser Welding Machine is one of the core highlights of this device. Laser welding has the advantages of high energy density, fast welding speed, and a small heat-affected zone. It can achieve high-quality connections between metal materials. The weld seam has high strength, an attractive appearance, and the deformation generated during the welding process is extremely small. Whether it is thin plate welding or thick plate welding, it can handle it easily.
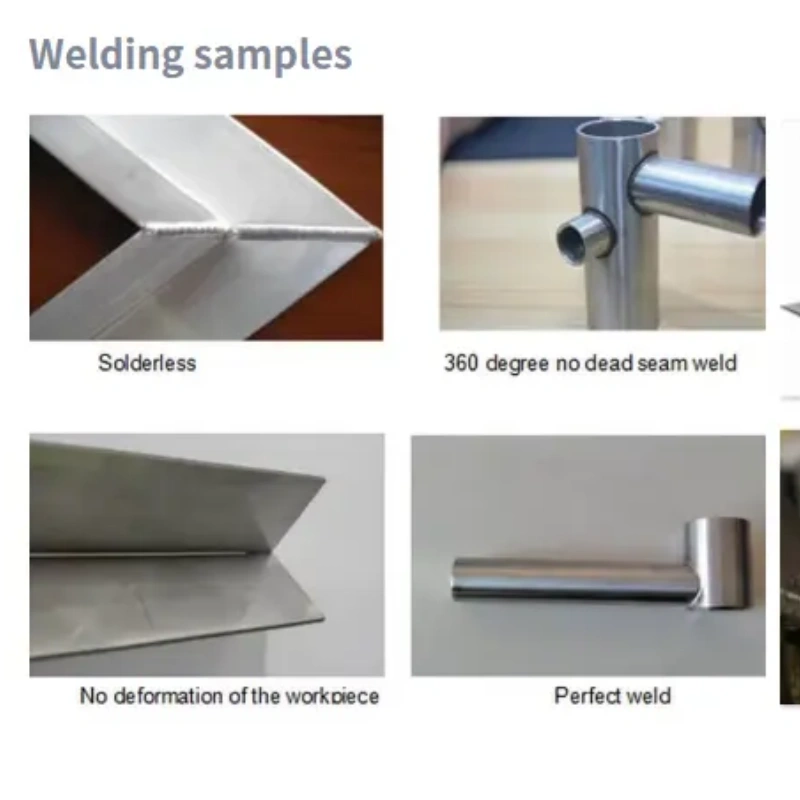
The laser weld seam cleaning function of the 4-in-1 Laser Welding Machine provides a powerful guarantee for the improvement of the quality after welding. During the welding process, impurities such as welding slag and scale may remain on the surface of the weld seam. If these impurities are not cleaned up in a timely manner, they will affect the appearance quality of the weld seam as well as subsequent processes such as painting and inspection. The laser weld seam cleaning function of this equipment can quickly and thoroughly remove these impurities, restoring the cleanliness of the weld seam surface and creating favorable conditions for subsequent processes.
laser equipment has a long service life and low maintenance costs. The laser, which is the core component of the equipment, adopts advanced technology and has high stability and reliability, enabling it to maintain stable performance during long-term operation. What’s more, the daily maintenance of the equipment is relatively simple. Regular cleaning and inspection are all that is needed to ensure the normal operation of the equipment, reducing the usage cost and maintenance time of the equipment.
The 4-in-1 Laser Welding Machine is widely used in many industries due to its multi – functionality, high efficiency, energy – saving, convenience, and flexibility, providing a powerful driving force for industrial upgrading and innovative development.
In the automotive manufacturing industry, it cleans parts’ surfaces to ensure assembly and painting quality, cuts and welds parts with high precision, enhancing the vehicle’s performance and safety.
In the aerospace field, it meets the high – precision processing requirements, welds hard – to – process materials with high quality, and the laser – cleaned parts are ready for re – processing and reuse.
In the electronics and electrical appliances industry, it processes electronic components with high precision and connects tiny parts. The laser cleaning function maintains devices, improving their performance and lifespan.
In the mechanical processing industry, it processes and repairs parts. Laser cutting makes complex – shaped parts, laser welding strengthens and repairs them, and laser cleaning readies parts for re – processing and reuse.
The emergence of the 4-in-1 Laser Welding Machine is undoubtedly a major innovation in the industrial field. With its characteristics of multi-functional integration, high efficiency, energy conservation, convenience, and flexibility, it has brought unprecedented convenience and efficiency improvement to numerous industries. With the continuous development of technology and the expansion of applications, it is believed that this device will play an even more important role in future industrial development and inject new vitality into industrial upgrading and sustainable development.