High Precision: “Artists” in the Micron World
One of the most amazing advantages of laser etching machines is its ultra-high processing accuracy, which can be called an “artist” in the micron world. Generally speaking, laser etching machines can easily achieve micron-level processing accuracy, and even in some advanced equipment, nano-level processing is not a problem. For example, some high-end laser etching machines can achieve a processing accuracy of 0.1 microns. What does this mean? The diameter of a hair is about 60-80 microns, which means that laser etching machines can perform precise processing on a scale much thinner than a hair.
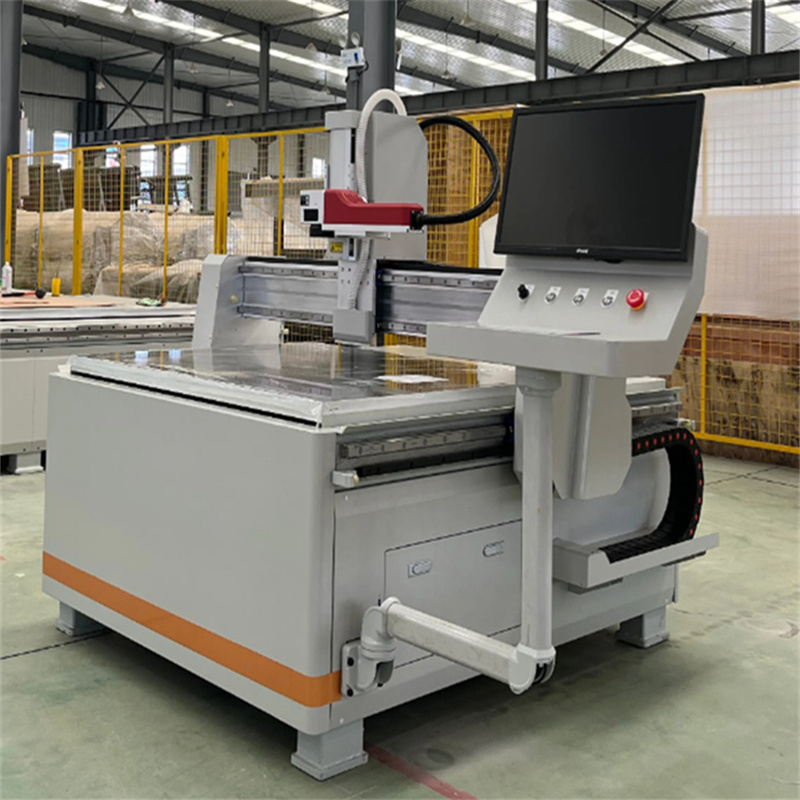
In the semiconductor industry, which requires extremely high precision, laser etching machines play a key role. Taking chip manufacturing as an example, the width of the circuit lines on the chip is getting narrower and narrower, and now it has entered the nano era. When manufacturing these ultra-fine circuits, laser etching machines can accurately control the position and depth of etching to ensure that each circuit component is accurately manufactured, thereby ensuring the high performance and stability of the chip. If traditional processing methods are used, it is difficult to achieve such high precision requirements, and the performance and reliability of the chip will be greatly reduced.
High Efficiency: A “Production Expert” Who Races Against Time
In the modern industry that pursues efficient production, the laser etching machine is undoubtedly a “production expert” who races against time. Compared with traditional mechanical processing, it has a huge advantage in processing speed. Traditional mechanical processing often requires cutting and grinding through the contact between the tool and the material. This process is relatively slow, and the tool also has the problem of wear and tear, and needs to be replaced frequently. The laser etching machine uses a high-energy laser beam to act on the surface of the material instantly, and the etching process can be completed almost instantly, which greatly saves time.
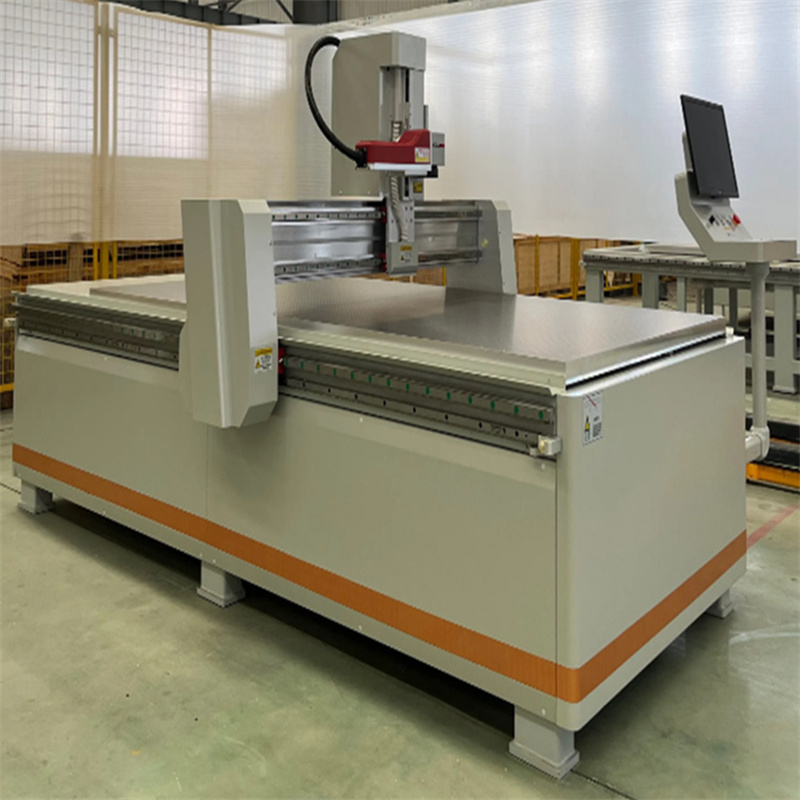
Take a factory that produces electronic product shells as an example. When using traditional mechanical engraving technology, it takes about 5-10 minutes to process the logo and pattern on a shell, and subsequent grinding, cleaning and other processes are also required. After using the laser etching machine, the same processing task can be completed in just a few tens of seconds, and the processing speed is increased several times or even dozens of times. Not only that, due to the high degree of automation of the laser etching machine, continuous and uninterrupted production can be achieved, further shortening the production cycle and reducing production costs. This enables companies to produce more products in a shorter time, respond quickly to market demand, and gain an advantage in the fierce market competition.
High Flexibility: A “Jack of All Trades” in Material Processing
The laser etching machine is like a “jack of all trades” in material processing, which can easily cope with the needs of various materials and processes. It can adapt to the etching processing of various materials such as metal, plastic, ceramic, glass, etc. by adjusting the laser power, pulse width, frequency and other parameters.
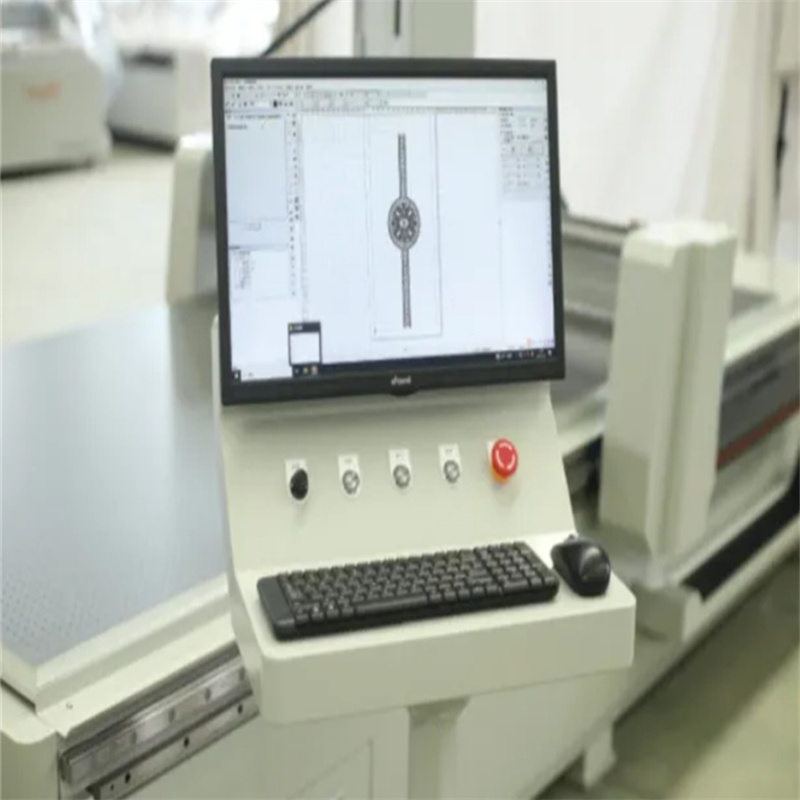
For metal materials, such as stainless steel, aluminum alloy, etc., the laser etching machine can etch exquisite patterns, logos and texts on their surfaces, while ensuring that the hardness and corrosion resistance of the metal surface are not affected. In electronic products, many of the brand logos and product models on the common metal shells are completed by laser etching machines. For plastic materials, laser etching can achieve fine engraving and cutting, and produce various unique shapes and textures, which are widely used in plastic crafts, toys and other fields. In the processing of ceramic and glass materials, the laser etching machine can achieve high-precision pattern etching without destroying the material structure, adding unique artistic charm to ceramic artworks and glass products. Whether it is a simple line or a complex three-dimensional pattern, the laser etching machine can perfectly present it with its high flexibility to meet the diverse needs of different customers.
Environmental Protection Pioneer: Practitioner of Green Production
Today, with the increasing awareness of environmental protection, the laser etching machine is still a well-deserved environmental protection pioneer and an active practitioner of green production. Compared with the traditional etching process, it has obvious environmental advantages. Traditional etching processes often require the use of a large number of chemical reagents, such as strong acids. These chemical reagents not only pose a potential threat to the health of operators, but also produce a large amount of wastewater, waste gas and waste residue during use. It takes a lot of cost to treat these wastes, and if they are not handled properly, they will also cause serious pollution to the environment.
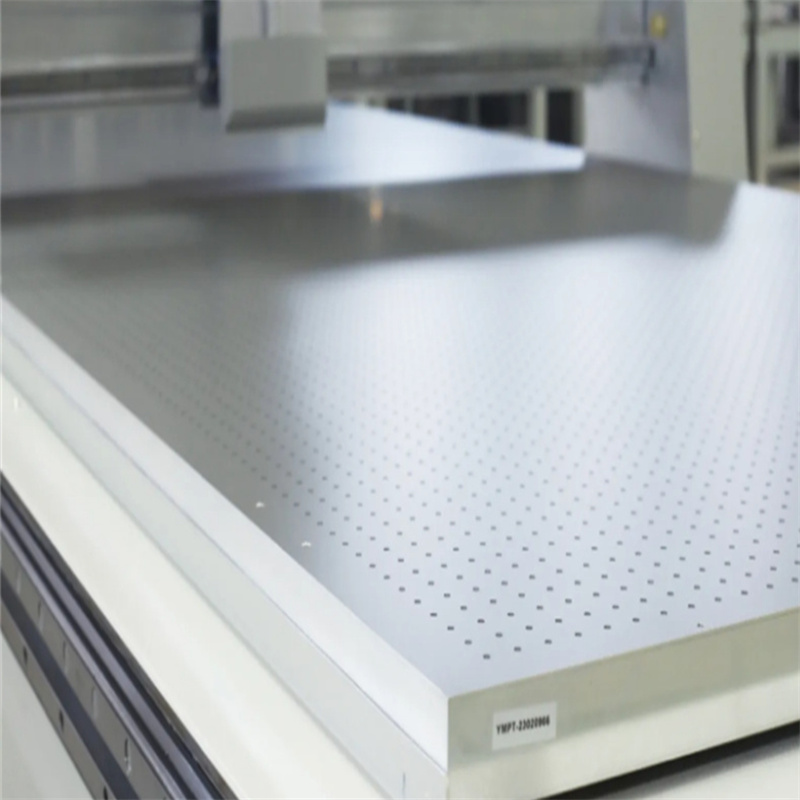
The laser etching machine does not need to use chemical reagents during operation. It directly uses the energy of the laser to act on the surface of the material to achieve etching, so it will not produce chemical pollution. At the same time, the waste generated during laser etching is also very small, mainly a small amount of vaporized material vapor, which can be easily collected and treated by simple waste gas treatment equipment. This not only conforms to the current development concept of green environmental protection, but also saves the cost of environmental protection treatment for enterprises, attracting more and more environmentally friendly enterprises to choose laser etching machines as their processing equipment.