Under the wave of Industry 4.0, laser welding technology is undergoing a leap from “tool innovation” to “intelligent system”. When the precision of the laser beam is deeply integrated with AI algorithms and IoT technology, a transformation that reshapes the logic of manufacturing in multiple fields is quietly taking place.
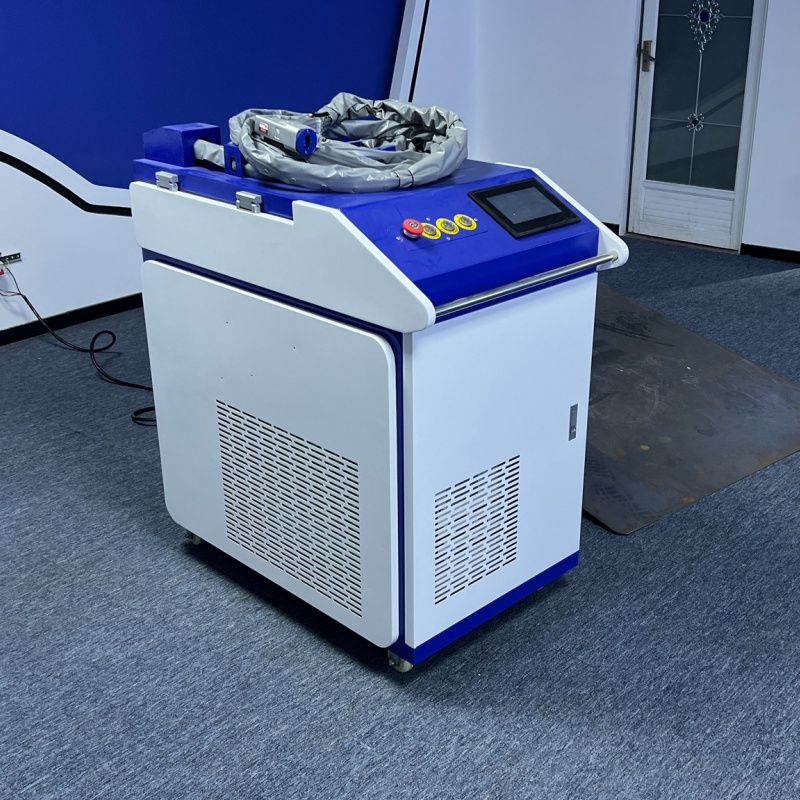
1. Intelligent Technology Reconstructs The Underlying Logic Of Welding Process
Traditional welding processes rely on manual experience to control parameters, while intelligent laser welding machines have achieved closed-loop control of “perception-decision-execution”. Taking the Qilin laser double-swing handheld welding machine as an example, its intelligent prevention and control system can monitor more than 20 core parameters such as laser power and welding speed in real time, and automatically match the optimal process solution through the built-in AI algorithm. When welding special curved workpieces, the built-in laser vision sensor of the equipment can scan the weld contour with an accuracy of 0.02mm, drive the double-swing head to complete the ±120° flexible swing angle, and improve the efficiency by more than 60% compared with traditional manual debugging. What is more noteworthy is that the BWT20S model supports remote IO module access to the factory MES system. Managers can monitor the equipment operation status of the workshop 50 kilometers away in real time through the cloud platform, and the welding quality data is synchronously generated into blockchain evidence to achieve zero error in process traceability.
2. Subversive Breakthroughs In Multi-field Manufacturing Scenarios
In the field of new energy vehicles, the intelligentization of laser welding is redefining the manufacturing standards of power batteries. The fully automatic laser welding production line introduced by a leading car company uses a 3D visual guidance system to achieve nano-level positioning of the welding position of the battery cell tabs, and uses pulsed laser technology to control the welding heat affected zone within 0.1mm, completely solving the hidden danger of electrolyte leakage caused by traditional resistance welding. Data shows that the single-shift production capacity of the production line has been increased to 8,000 modules/hour, and the welding defect rate is less than 0.03%, which has promoted the energy density of the battery pack to increase by 15%.
The aerospace field has witnessed the miracle of intelligent micro-nano welding. In the welding of micro inertial sensors used in satellite navigation systems, intelligent laser equipment uses picosecond laser technology to achieve the welding of 0.005mm ultra-thin metal films, and cooperates with vacuum environment chambers and laser Doppler vibrometers to suppress deformation of only 0.1μm during welding in real time. This “micro-level” precision control improves the environmental tolerance of aerospace electronic components by 3 orders of magnitude, ensuring the reliability of deep space exploration equipment.
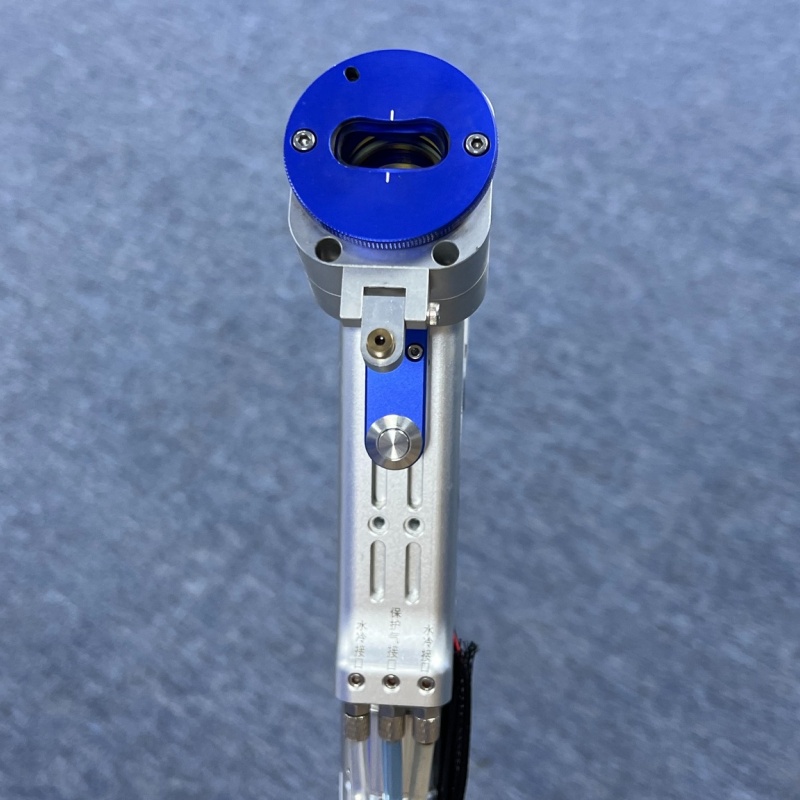
3. Two-way Rush Of Industrial Upgrading And Green Manufacturing
Intelligence is not only reflected in efficiency improvement, but also in building a sustainable manufacturing ecology. The laser welding intelligent unit introduced by a stainless steel processing company increases the laser energy utilization rate from 65% to 89% through an energy feedback system, saving 230,000 kWh of electricity annually; the matching smoke purification system adopts three-stage filtration + activated carbon adsorption technology to reduce the PM2.5 concentration in welding smoke from 800μg/m³ to 15μg/m³, reaching the cleanliness standard of food processing workshops. In addition, the equipment supports modular replacement of more than 95% of components, and the maintenance cycle is extended from 2,000 hours of traditional equipment to 8,000 hours, which greatly reduces the generation of industrial waste.
4. Future Vision: From Single-machine Intelligence To Ecological Collaboration
At present, the intelligentization of laser welding is evolving from a single device to a collaborative system of “welding robot + digital twin + edge computing”. The latest welding cloud platform released by Taier Heavy Industry has achieved cluster scheduling of 1,000 devices, and predicted equipment failures 72 hours in advance through the digital twin model, reducing maintenance costs by 40%. With the popularization of 5G+MEC technology, future laser welding systems will be deeply integrated into the industrial Internet, realizing dynamic planning of curved welding paths across workshops in shipbuilding, and completing cloud sharing of nano-level welding processes in the field of electronic packaging, and finally building a full-chain intelligent ecosystem of “demand perception-process optimization-production execution”.
When the laser beam becomes a bridge connecting the physical world and the digital world, intelligent welding equipment is rewriting the precision, speed and temperature of the manufacturing industry. This change is not only about the upgrade of a piece of equipment, but also heralds a paradigm revolution from “manufacturing” to “smart manufacturing” – in the invisible codes and light beams, a more efficient, greener and more resilient industrial future is coming.