In the wave of intelligent transformation of manufacturing industry, laser welding machines have become the core equipment for improving production efficiency. But facing the dazzling array of models on the market, how should enterprises choose the equipment that best suits their needs? This article disassembles the selection logic from six dimensions to help you make accurate decisions.
Anchoring Welding Needs: Dual Decoding Of Materials And Processes
The adaptability of laser welding depends first on the material properties and work piece requirements. For conventional metals such as ordinary steel and aluminum, fiber laser welding machines are cost-effective choices, which can easily meet the welding needs of 0.5-20mm thickness; and when welding sensitive materials such as stainless steel and titanium alloys, pulsed laser equipment can reduce thermal deformation, especially suitable for precision fields such as medical devices. It is worth noting that highly reflective materials such as copper and gold need to be equipped with anti-reflective coating laser heads-a power battery company once ignored this point, resulting in frequent damage to traditional optical fiber equipment. After replacing professional laser heads, the yield rate jumped from 78% to 99%.
If non-metallic materials are involved, CO₂laser welding machines are more advantageous. For example, in plastic welding of automotive interior parts, CO₂laser can achieve seamless welding, and the surface accuracy reaches the industry-leading level. In addition, the thickness of the workpiece directly determines the power selection: thin plates (<1mm) require pulsed lasers or galvanometer equipment (accuracy ±0.01mm), medium and thick plates (1-10mm) are suitable for continuous fiber lasers, and thick plates (>10mm) require high-power models above 5000W.
Matching Production Mode: Dynamic Balance Between Efficiency And Cost
The production scale directly affects the choice of equipment form. For single-piece customization or small-batch production, a handheld laser welding machine (50,000-200,000 yuan) is an ideal solution-after a bathroom company introduced it, the welding time of a single faucet was compressed from 8 minutes to 1.5 minutes, and the production capacity increased by 5 times while the labor cost was reduced by 60%. Large-scale assembly line production requires fully automatic welding lines, such as the 3C product shell welding scene. The production line with integrated robotic arms and visual inspection has an investment of more than one million, but can achieve 24-hour uninterrupted operation, and the defect rate is controlled within 0.03%.
The balance between speed and precision also needs to be considered: the precision electronics industry prefers galvanometer-type equipment (speed 500mm/s, positioning accuracy ±0.005mm), while the automotive parts field requires gantry-type models that take into account both efficiency and melting depth (speed 200-500mm/s, melting depth 3-8mm).
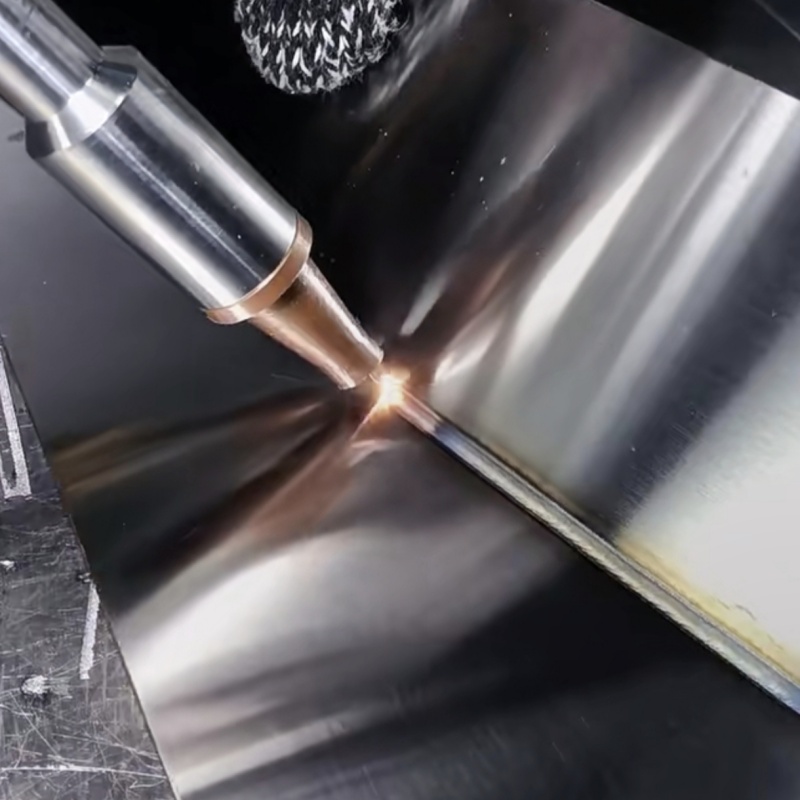
Penetrating The Cost Fog: Full-cycle Accounting From Procurement To Operation And Maintenance
Equipment procurement needs to jump out of the “price trap” and pay attention to the full life cycle cost. Entry-level handheld devices only cost 50,000 to 300,000 yuan, which is suitable for small and micro enterprises to test the waters; medium-sized enterprises can choose fully automatic models of 500,000 to 5 million yuan for large-scale production; and giant companies such as automobiles and aerospace need to invest more than 5 million yuan to deploy industrial robot integration solutions.
Hidden costs are often overlooked: Fiber laser equipment consumes 70% less energy than traditional argon arc welding. Taking a 1000W model as an example, it consumes only 1.5 degrees of electricity per hour, saving more than 30,000 yuan in electricity bills per year; YAG lasers require regular replacement of xenon lamps (costing 20,000-50,000 yuan/time), while fiber lasers have a lifespan of 100,000 hours and are almost maintenance-free. In addition, laser welding does not require welding rods, directly saving 15-20% of consumable costs.
Deconstructing Technical Configuration: The Selection Code Of Core Components
Laser type is the core of technical selection: fiber lasers have an electro-optical conversion efficiency of more than 30%, a long life, and are suitable for metal welding (IPG, Raycus and other brands occupy the mainstream market); CO₂ lasers focus on non-metallic fields (such as the Han’s Laser G4020HF model); disk lasers have excellent beam quality and are often used for precision welding (Trumpf TruDisk series).
Auxiliary modules determine the application boundary: the visual positioning system can control the weld recognition error within 0.1mm, which is suitable for complex curved surface welding; the weld tracker compensates for the workpiece error in real time, and performs well in the splicing of automotive cover parts; environmentally friendly enterprises need to pay attention to smoke purification devices, such as high-efficiency filtration of hydrogen fluoride gas when welding aluminum alloys to ensure compliance with ISO 11541 standards.
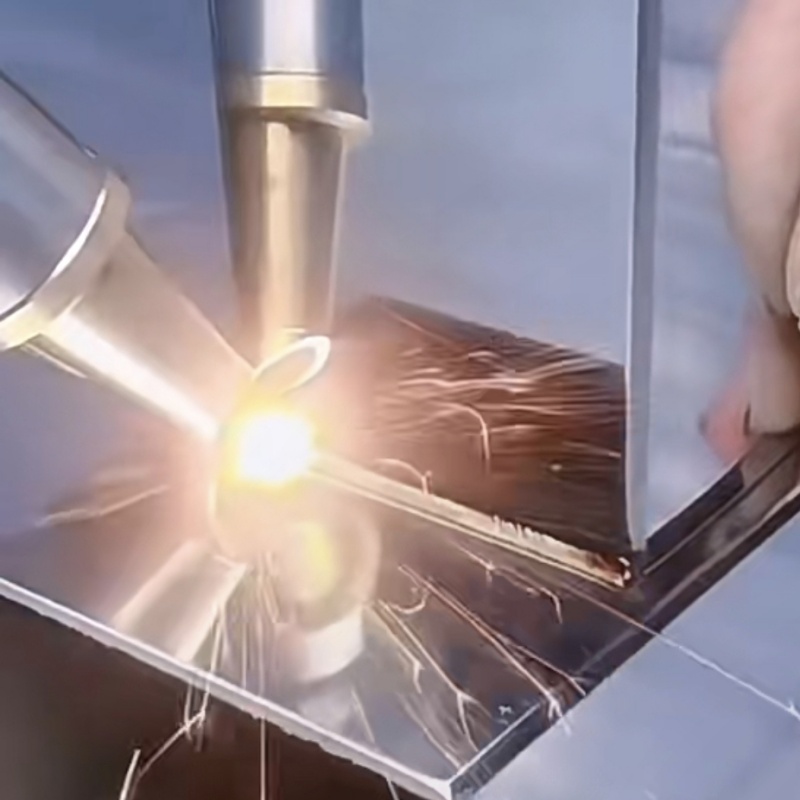
Verify The Strength Of Suppliers: Double Verification From Cases To Services
Prefer suppliers with mature cases in the target field-if involved in power battery welding, you can check whether they have served leading companies such as CATL; in the field of medical devices, it is necessary to confirm whether the equipment has passed GMP certification. The response speed of after-sales service is crucial. Companies such as Han’s Laser provide “24-hour door-to-door + free training” services. The warranty period for core components is usually 2-3 years, and the warranty period for the galvanometer system is 1 year.
Forward-looking Policies And Environmental Protection:The Invisible Threshold Of Sustainable Development
Equipment energy efficiency must comply with GB 19714 standards. Level 1 energy efficiency models save more than 40% energy compared to level 3 models, and long-term use can significantly reduce carbon footprint. In terms of environmental compliance, closed welding cabins and multi-stage fume purification systems have become standard. Some regions have included welding fume emissions in the scope of environmental protection tax collection. Early layout can avoid policy risks.
Decision-making Tool: Selection Checklist
Clarify material type (metal/non-metal) and thickness range
Evaluate daily production capacity requirements (single piece/batch/assembly line)
Calculate 3-year total holding costs (purchase + energy consumption + maintenance)
Verify supplier similar cases and after-sales response speed
Confirm equipment energy efficiency and environmental certification documents
The essence of laser welding machine selection is “demand translation” – converting the company’s process pain points and production capacity goals into technical parameters and configuration combinations of equipment. Through systematic evaluation and avoiding the traps of “high configuration and low usage” or “a small horse pulling a big cart”, the laser beam can become the fulcrum for leveraging efficiency growth and lay a solid equipment foundation for intelligent manufacturing.