In today’s rapidly evolving technological landscape, laser technology has been widely applied across various fields, ranging from healthcare and communication to entertainment and industrial manufacturing. Among these applications, laser cutting machines, as a crucial manifestation of laser technology, are quietly revolutionizing the manufacturing industry, emerging as indispensable precision “tailors” in modern manufacturing.
I. Working Principle of Laser Cutting
The working principle of laser cutting machines is rooted in the high energy density characteristic of lasers. In simple terms, a laser beam with high energy density is directed at the workpiece. The irradiated material rapidly melts, vaporizes, or reaches its ignition point. Simultaneously, high-speed gas flow coaxial with the beam blows away the molten substances, thus achieving the cutting of the workpiece. This process is akin to using an extremely fine and powerful “light knife” to cut materials.
Specifically, when the laser beam generated by the laser generator is focused onto the surface of the workpiece through the optical system, the material absorbs the laser energy, causing its temperature to rise sharply. In an extremely short period, the material reaches its melting point or even boiling point, undergoing melting and vaporization. At this moment, high-speed gas, such as oxygen, nitrogen, or compressed air, is ejected from the nozzle coaxial with the laser beam. These high-speed gases quickly blow away the melted and vaporized material from the cutting area, forming a narrow slit in the material and completing the cutting process.
II. Classification of Laser Cutting
Based on the different reactions of materials during the cutting process and the use of auxiliary gases, laser cutting can be mainly categorized into the following four types:
Laser Vaporization Cutting: This cutting method uses a high-energy-density laser beam to heat the workpiece, causing the temperature to rise rapidly and reach the boiling point of the material in a very short time. The material then begins to vaporize, forming vapor. Due to the high ejection speed of the vapor, a slit is formed in the material as the vapor is expelled. However, the heat of vaporization of materials is generally large, so laser vaporization cutting requires a significant amount of power and power density. It is often used in scenarios where extremely high cutting precision is required and the materials are thin, such as the processing of certain electronic components.
Laser Melting Cutting: In laser melting cutting, the metal material is first heated to a molten state by the laser. Then, non-oxidizing gases (such as Ar, He, N, etc.) are blown through the nozzle coaxial with the beam. These gases, driven by strong pressure, expel the liquid metal, thereby forming a slit. Unlike laser vaporization cutting, laser melting cutting does not require the metal to be completely vaporized, and the required energy is only about one-tenth of that of vaporization cutting. This method is mainly used for cutting materials that are not easily oxidized or active metals, such as stainless steel, titanium, aluminum, and their alloys, which are widely used in the industry.
Laser Oxygen Cutting: Its principle is similar to traditional oxyacetylene cutting. In laser oxygen cutting, the laser serves as a preheating heat source, and active gases such as oxygen are used as the cutting gas. The ejected oxygen not only reacts with the cutting metal, releasing a large amount of oxidation heat, but also blows the molten oxides and melt from the reaction zone, thus forming a slit in the metal. Due to the large amount of heat generated by the oxidation reaction during the cutting process, the energy required for laser oxygen cutting is only half of that for melting cutting, and the cutting speed is much faster than that of laser vaporization cutting and melting cutting. This cutting method is mainly used for cutting oxidizable metal materials such as carbon steel, titanium steel, and heat-treated steel, and is widely applied in industries such as construction and machinery manufacturing.
Laser Dicing and Controlled Fracturing: Laser dicing involves scanning the surface of brittle materials with a high-energy-density laser, causing the material to evaporate and form a small groove. Then, by applying a certain pressure, the brittle material will crack along the groove. Lasers commonly used for laser dicing are generally Q-switched lasers and CO₂ lasers. Controlled fracturing, on the other hand, utilizes the steep temperature distribution generated during laser grooving to create local thermal stress in the brittle material, causing the material to break along the groove. This cutting method plays an important role in fields such as semiconductor manufacturing and electronic device production, for example, in the cutting and processing of brittle materials like silicon wafers.
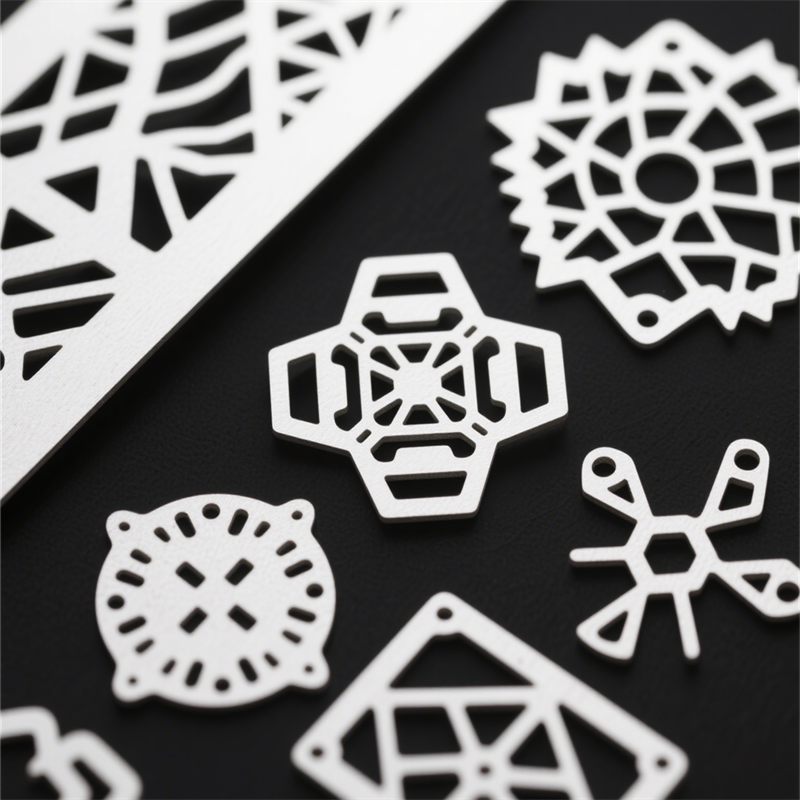
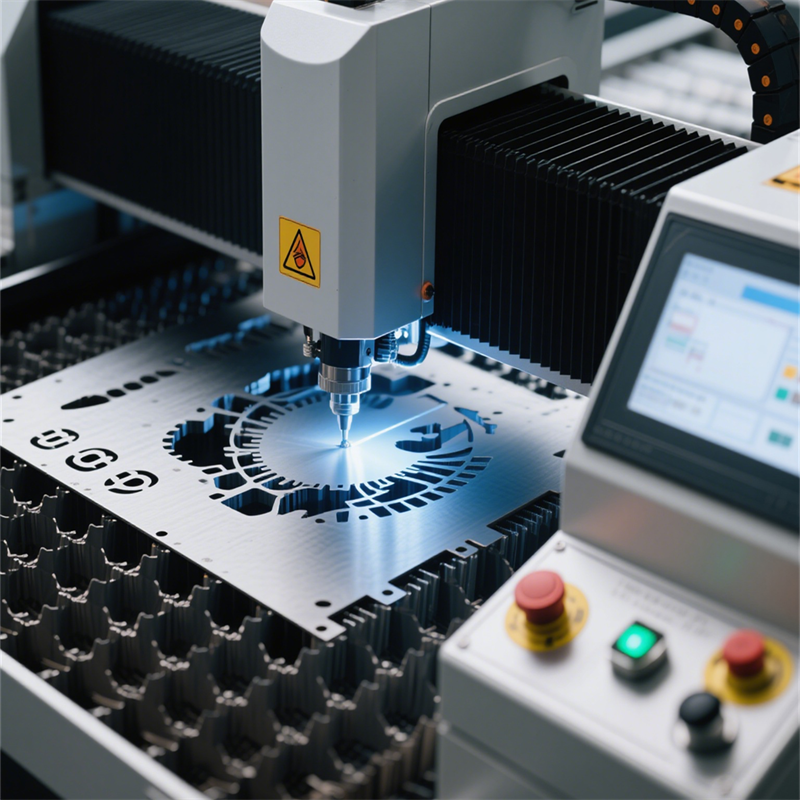
III. Components of Laser Cutting Machines
A complete laser cutting machine usually consists of several key components, each playing an indispensable role:
Laser Generator: This is the core component of the laser cutting machine, responsible for generating a laser beam with high energy density. Different types of laser generators produce laser beams with varying characteristics. Common ones include carbon dioxide lasers, fiber lasers, and YAG lasers. Carbon dioxide lasers have a wide output power range and are suitable for cutting a variety of materials, including non-metallic materials and some metallic materials. Fiber lasers offer advantages such as high conversion efficiency, good beam quality, and easy maintenance, and perform exceptionally well in cutting metallic materials, especially for medium and thick plates. YAG lasers are often used in precision machining applications where high pulse energy and good beam quality are required.
Beam Delivery System: Composed of a series of optical components such as mirrors and lenses, its main task is to transmit the laser beam generated by the laser generator and focus it precisely onto the surface of the workpiece. During this process, the beam delivery system must ensure uniform energy distribution of the laser beam and high focusing accuracy to guarantee cutting quality. For example, by accurately adjusting the angle of the mirrors and the focal length of the lenses, the laser beam can form an extremely small spot on the workpiece surface, enabling high-precision cutting.
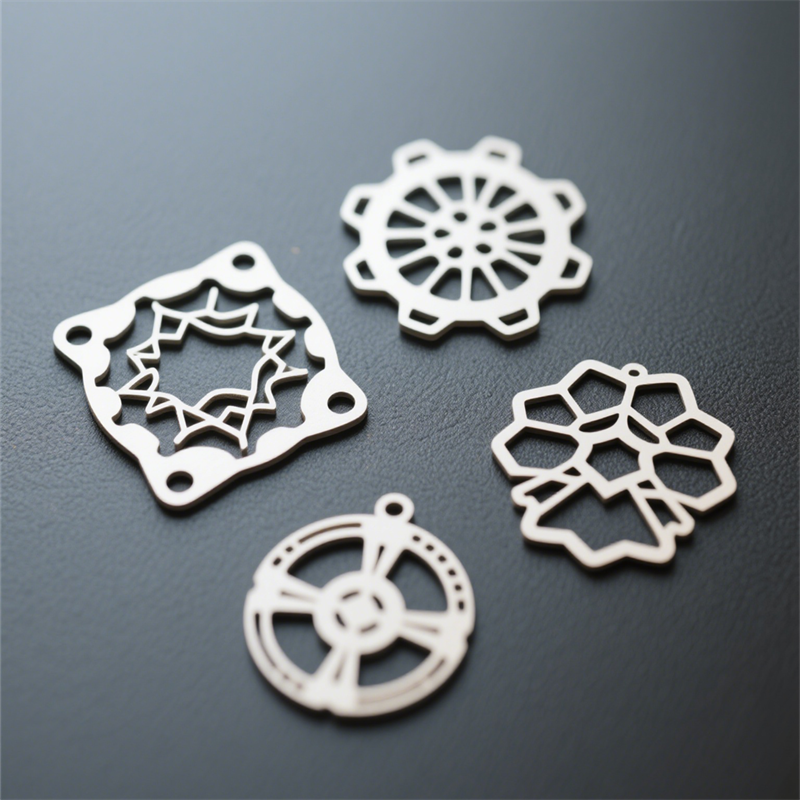
Cutting Head: Installed at the end of the beam delivery system, it contains important components such as focusing lenses and nozzles. The design and performance of the cutting head directly affect the cutting quality and efficiency. The focusing lens further focuses the laser beam to an even smaller spot size, increasing the energy density. The nozzle is used to eject high-pressure auxiliary gas into the cutting area, helping to blow away the molten substances and protecting the focusing lens from splashes. Different cutting processes and materials require the selection of appropriate cutting heads. For example, for thick plate cutting, nozzles with larger diameters and specially designed focusing lenses may be needed to ensure effective gas ejection and good focusing of the laser beam.
Worktable: Used to place the workpiece to be cut, it can achieve precise movement under the control of the numerical control system. The worktable is usually equipped with high-precision guide rails and transmission devices, enabling rapid and smooth movement of the workpiece in the X and Y directions to meet different cutting path requirements. Some high-end laser cutting machine worktables also have a Z-axis adjustment function, which can automatically adjust the distance between the cutting head and the workpiece according to the thickness of the workpiece, ensuring the stability of the cutting process. In addition, to improve production efficiency, some worktables are equipped with automatic loading and unloading devices for automated production.
Control System: It can be regarded as the “brain” of the laser cutting machine, responsible for precisely controlling the entire cutting process. Operators input parameters such as cutting graphics, dimensions, cutting speed, and laser power through the control system. Based on these instructions, the control system precisely controls the working state of the laser generator, the adjustment of the beam delivery system, the movement of the cutting head, and the movement of the worktable. Advanced control systems also have intelligent functions, such as automatically optimizing the cutting path, real-time monitoring of parameter changes during the cutting process and making adjustments, to improve cutting efficiency and quality and reduce material waste.
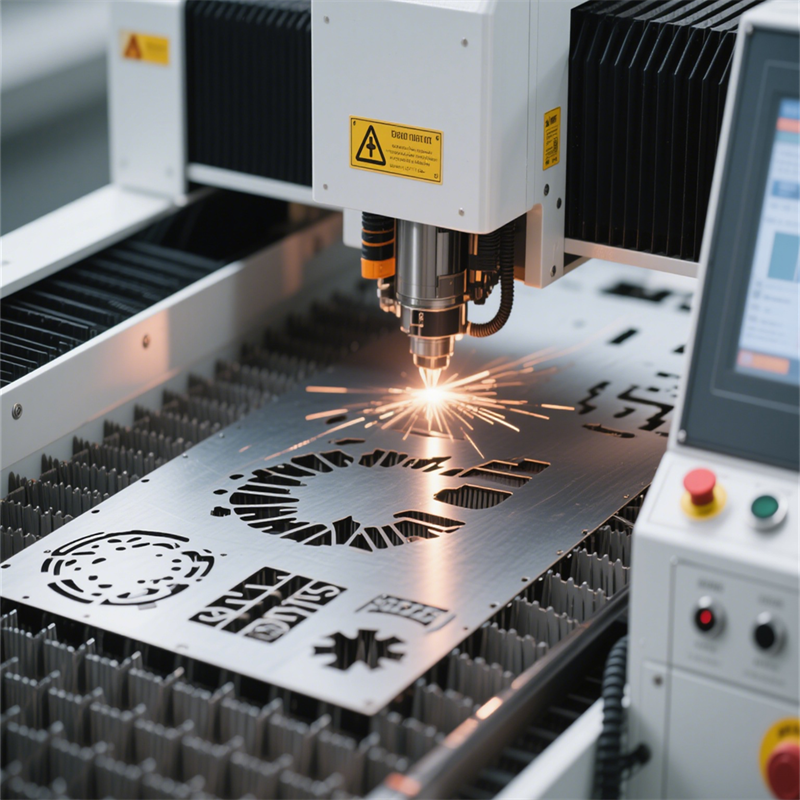