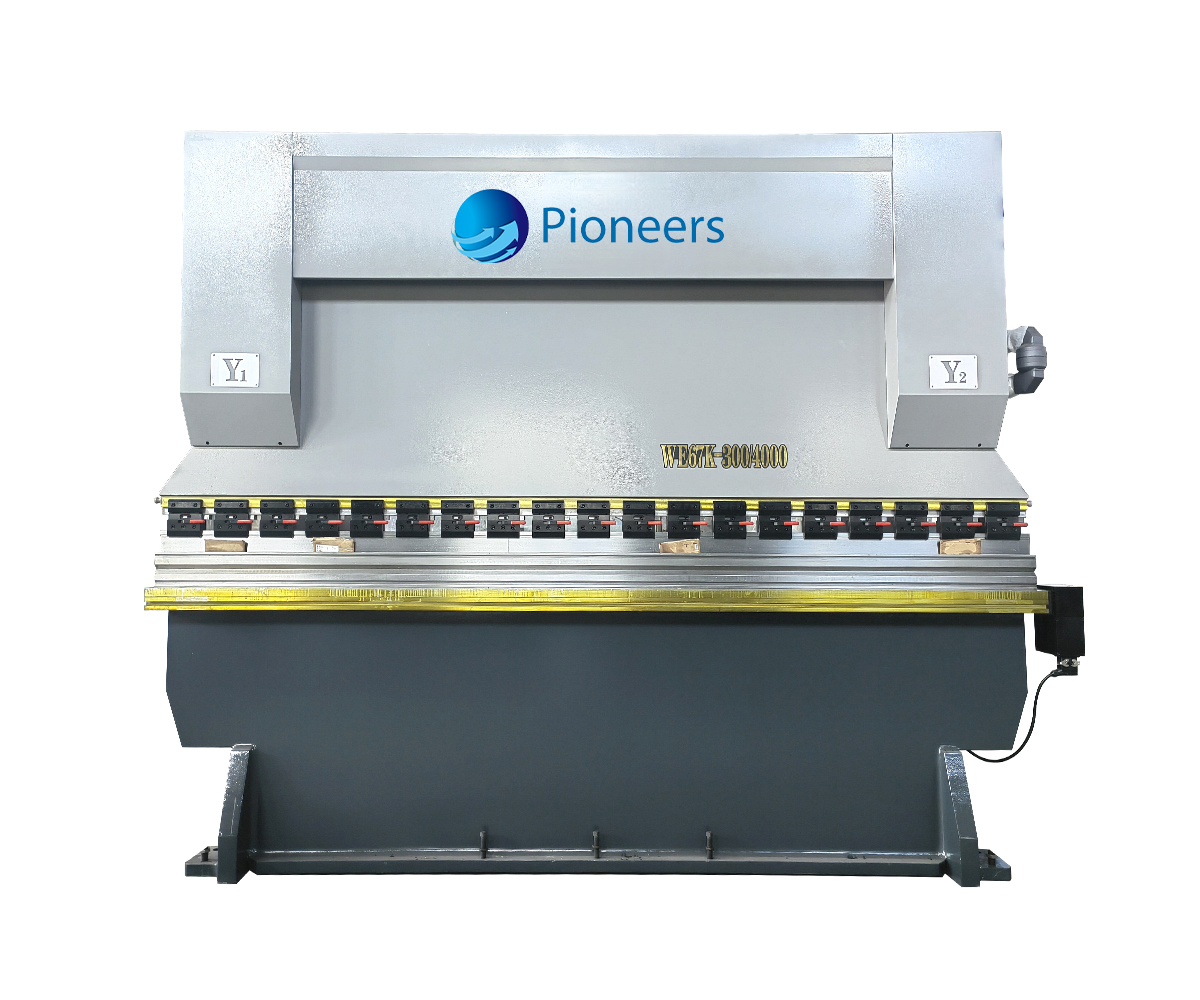
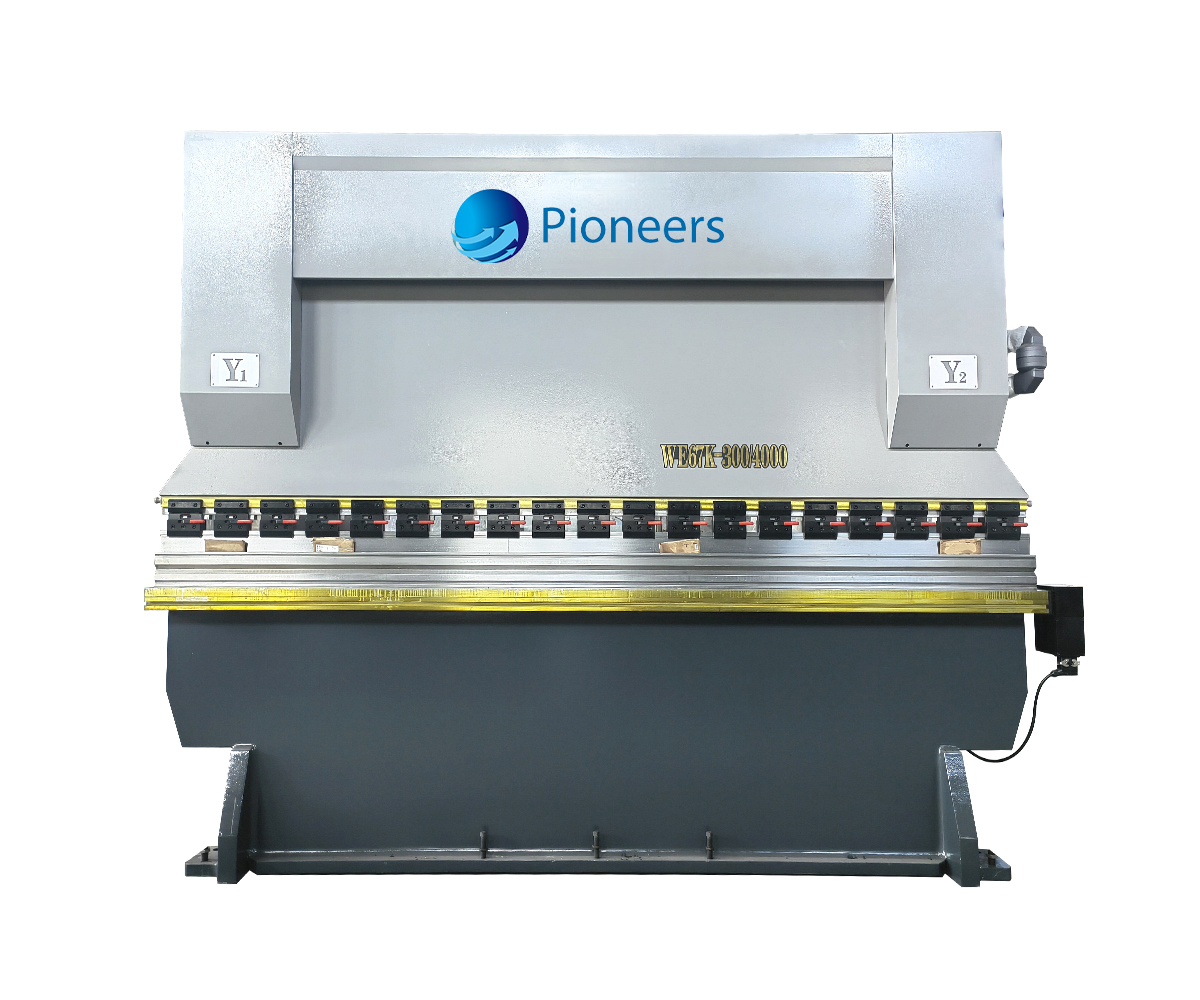
body .block-social .twitter{ background-image: url(data:image/svg+xml;base64,PHN2ZyB4bWxucz0iaHR0cDovL3d3dy53My5vcmcvMjAwMC9zdmciIHdpZHRoPSIxNiIgaGVpZ2h0PSIxNiIgZmlsbD0iY3VycmVudENvbG9yIiBjbGFzcz0iYmkgYmktdHdpdHRlci14IiB2aWV3Qm94PSIwIDAgMTYgMTYiPgogIDxwYXRoIGQ9Ik0xMi42Ljc1aDIuNDU0bC01LjM2IDYuMTQyTDE2IDE1LjI1aC00LjkzN2wtMy44NjctNS4wNy00LjQyNSA1LjA3SC4zMTZsNS43MzMtNi41N0wwIC43NWg1LjA2M2wzLjQ5NSA0LjYzM0wxMi42MDEuNzVabS0uODYgMTMuMDI4aDEuMzZMNC4zMjMgMi4xNDVIMi44NjV6Ii8+Cjwvc3ZnPg==); background-position: 5px 5px; background-size: 25px; color: white; background-position: 5px 6px; opacity: 0.5; } #footer #copyright .col-xl-2{ width:320px; }.goog-te-gadget{ height: 30px; overflow: hidden ; } body #topcat .categories ul.categories-top li a{ position: relative; top: 0; color: #fff; display: block; border-left: 1px solid #ffffff73; padding: 3px 10px; height: 76px; align-items: center; display: flex; font-size: 13.5px; } #main .block-category h1{ font-size:29px; } body{ margin:0; } .header-banner{ padding:5px 0; background:#2190ff; text-align:center; color:#fff; } @media screen and (max-width: 750px ){ #main .block-category h1{ font-size:20px; } }
CNC technology: Through programming, automatic processing is achieved, which greatly improves production efficiency. At the same time, the CNC system also has a variety of bending modes to meet the bending needs of different shapes and angles. Synchronous torque technology: Through precise torque control, it ensures that the plate is evenly stressed during the bending process to avoid problems such as deformation or distortion. This technology also enables the equipment to adapt to plates of different thicknesses and materials, improving the versatility and flexibility of the equipment. Safety protection measures: The equipment has a variety of safety protection measures, such as overload protection, emergency stop, etc., to ensure the safety of operators. Simple maintenance: The maintenance of the equipment is relatively simple, which reduces the cost of use.
“Shortcut” touch navigation
10.1″ industrial-grade TFT touch screen
Up to 4-axis control (Y1, Y2 + 2 auxiliary axes)
Deflection compensation control with mold/material/product library
Large arc programming function
Advanced Y-axis control algorithm, can control both closed-loop valves and open-loop valves.
Internal storage capacity 1 GB
USB peripheral interface
USB data backup/restore
Profile-53TL offline programming software
■ Back gauge fingers with two gauging steps used one for short and the other for long bending depths.
■ Back Gauge positioning fingers move along linear bearings with ±0.10mm. positioning tolerance
■The equipped standard Dies, special non-standard mold is available under client’s requirement according to real workpiece situation.
■Upper and buttom die can be sectioned according to customer’s requirement.
No. | Name | Value | Unit |
1 | Nominal pressure | 4000 | KN |
2 | Length of working table | 4000 | mm |
3 | Distance between uprights | 3150 | mm |
4 | Throat depth | 400 | mm |
5 | Storke | 300 | mm |
6 | Open height | 650 | mm |
7 | Motor power | 22 | KW |
8 | Gear pump | 50 | L |
During the bending process of the workpiece, the force generated when the plate is bent causes the lower surface of the slider to deform concavely due to the maximum force on the oil cylinders at both ends of the slider. The deformation of the middle part of the slider is large. In order to eliminate the adverse effects of slider deformation, it is necessary to compensate for the deflection deformation of the slider. The convex worktable mechanical compensation mechanism causes the middle part of the worktable to produce upward elastic deformation to offset the deformation of the machine tool slider, ensure the accuracy of the machining joint surface, and improve the accuracy of the workpiece. The bending machine uses mechanical compensation for the worktable. When the slider stops at the top dead point, the CNC system automatically calculates the compensation amount based on the thickness, length, and selected mold of the bending material. The system module controls the forward and reverse direction of the motor to adjust the compensation deformation, and then feeds back the changes in the position of the upper and lower pads through a potentiometer.
phone: +8613791007598
[email protected]