In the field of industrial manufacturing, the efficiency and flexibility of welding processes have always been the key to improving production efficiency. As a new generation of integrated welding equipment, the 4-in-1 welding machine integrates multiple welding functions into one through innovative technology, redefining the standards of modern welding operations. Its core advantages are reflected in the following four dimensions:
1. Multifunctional Integration: One Device Covers All Scene Requirements
Traditional welding operations often require the cooperation of multiple single-function equipment, which not only takes up a lot of space, but also requires frequent switching of equipment, affecting the production rhythm. The 4-in-1 welding machine has a breakthrough integration of argon arc welding, carbon dioxide shielded welding, manual arc welding, gas shielded welding and other processes, and can flexibly switch modes for different materials such as stainless steel, carbon steel, aluminum alloy, and various workpiece types such as thin plates and thick plates. Whether it is the delicate welding of precision electronic components or the high-strength connection of large steel structures, one device can cover the entire process, completely solving the problem of resource waste of “one machine for one use”.
2. Efficiency Leap: Intelligent Control Shortens Operation Cycle
The equipment is equipped with an intelligent control system that can automatically match welding parameters (such as current, voltage, gas flow, etc.) to reduce manual debugging time. Taking stainless steel sheet welding as an example, traditional equipment needs to debug parameters in stages, and a single operation takes about 15 minutes. The 4-in-1 welding machine can be started with one button through a preset program, and it only takes 8 minutes to complete under the same working conditions, and the efficiency is increased by nearly 50%. In addition, its integrated design reduces the frequency of equipment start-up and shutdown and replacement of welding guns, further compressing non-production time, which is especially suitable for assembly line operation scenarios.
3. Cost Optimization: Cost Reduction And Efficiency Improvement
From the perspective of enterprise operation, the economic efficiency of the 4-in-1 welding machine is reflected in the dual optimization of initial procurement cost and later operation and maintenance cost: Sharp reduction in equipment investment: one device replaces four traditional welding machines, directly reducing hardware procurement costs by more than 70%, while saving 30% of workshop space; Labor cost compression: no need to equip operators of multiple trades, a single technician can complete the entire process operation, and labor costs are reduced by about 40%; Reduced consumable loss: the intelligent system accurately controls the welding energy output, and the utilization rate of consumables such as welding wire and gas is increased by 20%-30%, which saves significant money in long-term use.
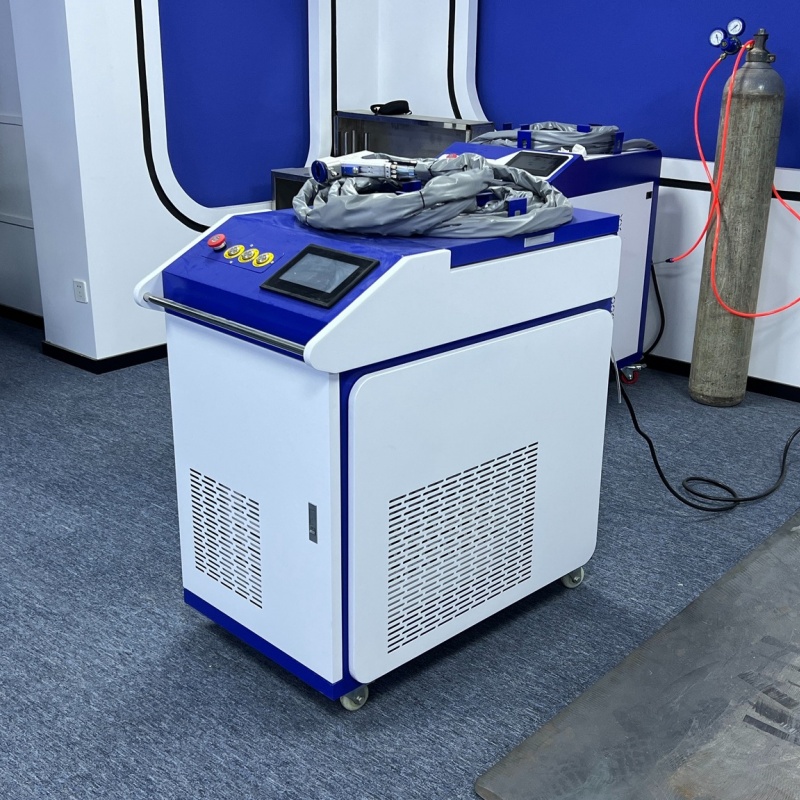
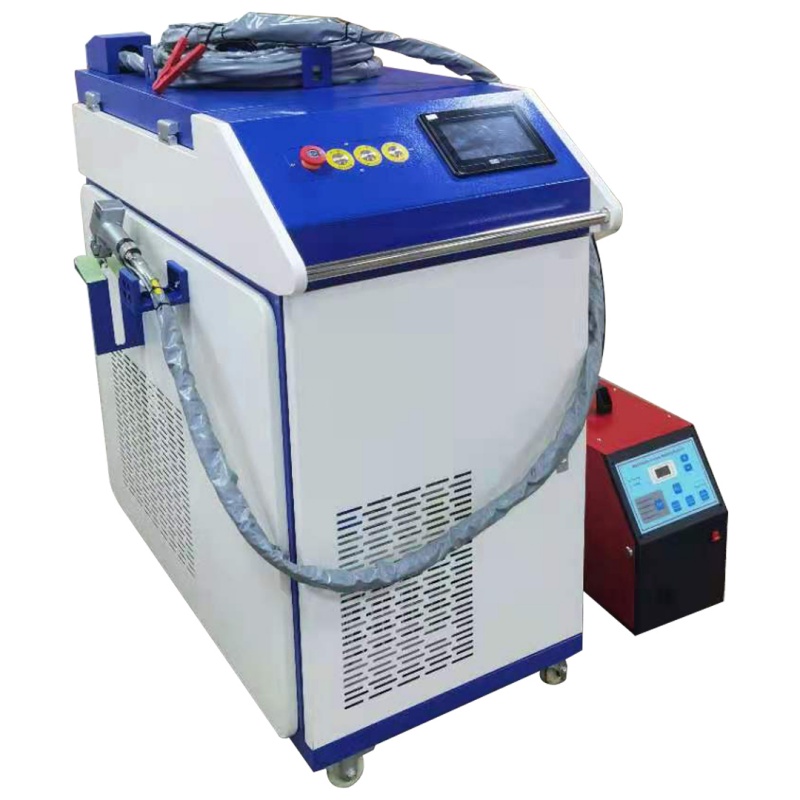
4. Friendly Operation: Low Threshold And High Stability
For novice technicians, traditional multi-device switching is prone to welding defects (such as welding penetration, pores, lack of fusion, etc.) due to incorrect parameter settings. The 4-in-1 welding machine supports one-click call of preset solutions through a graphical operation interface and process parameter memory function, greatly reducing the operation threshold. At the same time, the equipment has a built-in intelligent error correction system, which can monitor the welding process in real time and automatically adjust parameters to ensure uniform weld formation and stable mechanical properties. Even under complex working conditions, the yield rate can be maintained at over 98%, reducing rework costs and quality risks.
5. Scenario Adaptation: An All-Round Player for All-Industry Applications
The multifunctional characteristics of the 4-in-1 welding machine make it a “universal tool” across industries: Mechanical Manufacturing: Suitable for scenes such as component assembly and box welding, compatible with mixed welding of multiple materials; Pressure vessels: Meet high-precision welding requirements such as high-pressure pipelines and storage tanks to ensure sealing and safety; Automobile Manufacturing: Can complete rapid welding of body frames and chassis structures, adapting to the lightweight trend of aluminum alloys; Hardware Processing: Support small-batch customized production and flexibly respond to diversified order requirements.