With its processing characteristics of high precision, high efficiency and high flexibility, the metal tube and pipe laser cutting machine has become a key device for the transformation and upgrading of many industries, profoundly influencing the production mode and development trend of modern manufacturing.
- Core of the Technology: Decoding the Mysteries of Laser Cutting
The working principle of the metal tube and pipe laser cutting machine is based on a laser beam with high energy density. When the laser beam is focused on the surface of the metal tube or pipe, the instantaneously generated high temperature causes the material to melt rapidly or even vaporize. At the same time, with the help of auxiliary gas, the molten substance is blown away from the cutting area, thus forming a precise cutting seam. Compared with traditional mechanical cutting methods, laser cutting is a non-contact processing method. This not only avoids the processing errors caused by tool wear but also enables an extremely small cutting seam width, which can usually reach 0.1 to 0.3 millimeters, greatly improving the processing precision.
In addition, the advanced numerical control system endows the metal tube and pipe laser cutting machine with powerful automation capabilities. Operators only need to draw the cutting pattern on the computer or import the CAD drawing, and the equipment can quickly analyze the instructions and precisely control the laser head to move along the preset path, enabling the efficient cutting of complex patterns and irregular structures. Some high-end models are also equipped with an automatic feeding system, a pipe alignment system, and a scrap recycling system, which further improves the production continuity and material utilization rate.
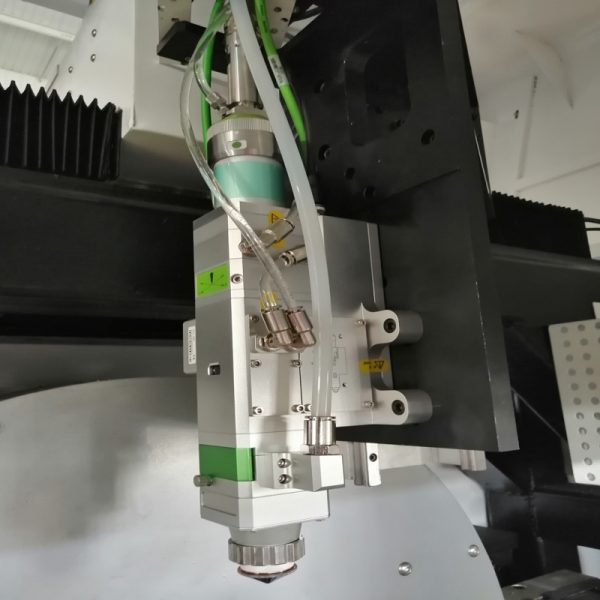
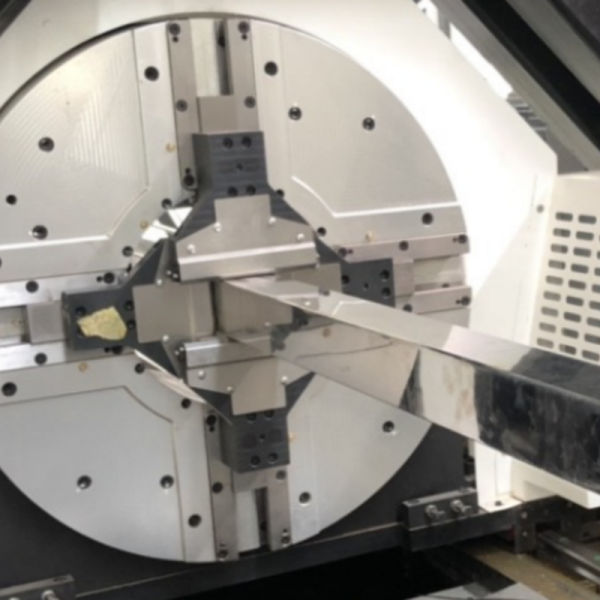
- Application panorama: Shining in multiple fields
In the aerospace field, the metal tube and pipe laser cutting machine can be regarded as the “guardian of precision”. Components such as the combustion chamber parts of aircraft engines and the hydraulic pipelines of wings often use high-strength and difficult-to-machine materials like titanium alloys and nickel-based alloys. Laser cutting technology can process these tubes into complex curved surfaces and precise hole system structures without causing thermal deformation, ensuring the lightweight and high reliability of aerospace components, and providing a guarantee for the safe flight of aircraft and the improvement of fuel efficiency.
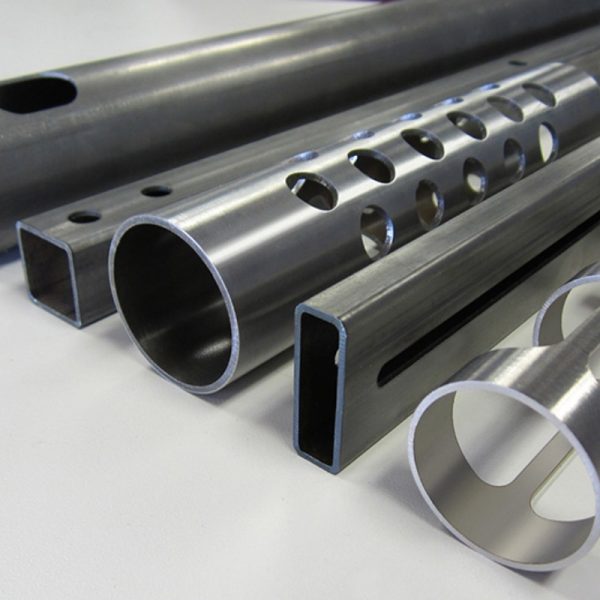
In the automotive manufacturing industry, the metal tube and pipe laser cutting machine serves as an “efficiency booster”. From the suspension brackets and anti-collision beams of the automobile chassis to the silencer pipes of the exhaust system, laser cutting technology can quickly complete the cutting tasks. After a well-known automobile manufacturer introduced laser cutting equipment, the production cycle of key body parts was shortened by 30%, and the scrap rate was reduced to below 1%, significantly improving production efficiency and product quality. At the same time, laser cutting can also achieve three-dimensional cutting of tubes, meeting the increasingly complex styling requirements in automobile design.
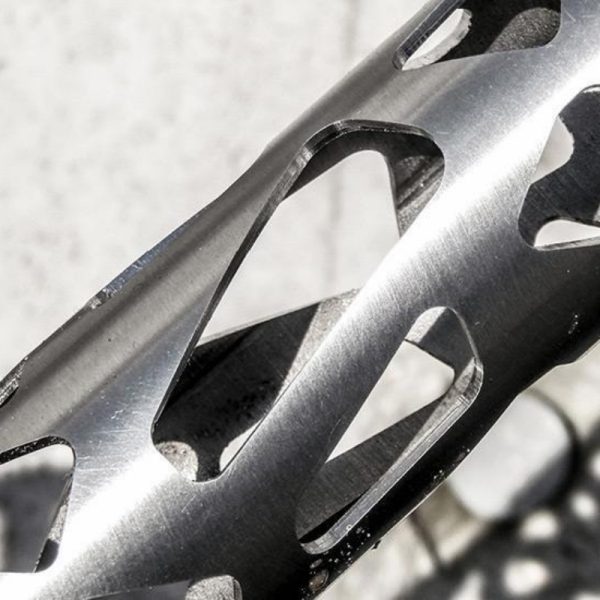
The energy industry has also benefited a great deal from the application of metal tube and pipe laser cutting machines. In the field of oil and gas transportation, laser cutting can accurately process large-diameter and thick-walled alloy steel pipes, ensuring the tightness and strength of the pipeline connection parts and reducing the risk of leakage during transportation. In the new energy industry, such as the processing of the internal support structures of the towers of wind power generation equipment and the solar photovoltaic brackets, the laser cutting machine, with its characteristics of high efficiency and flexibility, provides strong support for the rapid construction of new energy projects.
In kitchenware production, the laser cutting machine can cut stainless steel tubes into various shapes for making cabinet frames, sink brackets, etc. The cutting surface is smooth without burrs, and there is no need for excessive subsequent processing. In terms of bathroom products, for metal pipe fittings such as showerhead brackets and towel racks, laser cutting can achieve diversified styling designs to meet consumers’ dual needs for aesthetics and practicality.
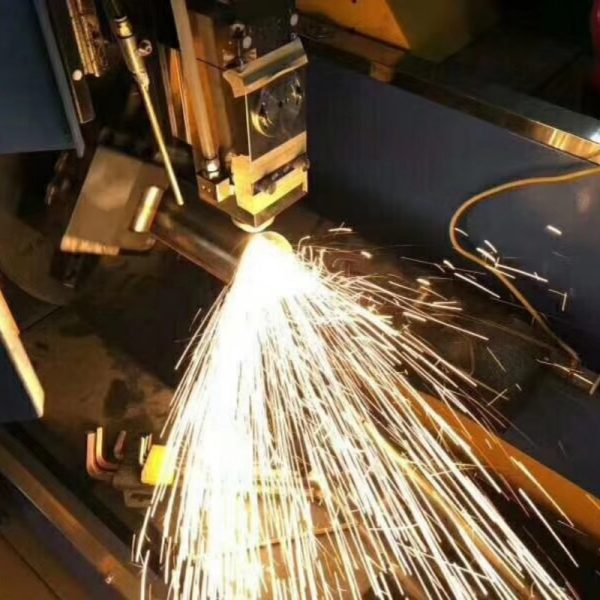
Looking ahead, metal tube and pipe laser cutting machines will develop towards higher power, higher precision, and greater intelligence. The continuous innovation of fiber laser technology will further improve cutting efficiency and processing quality. The in-depth integration with robot technology can build automated cutting production lines, enabling unmanned operation of the entire process of tube feeding, cutting, and sorting. The application of Internet of Things (IoT) and big data technologies allows for real-time monitoring of equipment operation status and data analysis, providing early warnings of faults and optimizing production management.
Under the guidance of the concept of green manufacturing, new environmentally friendly cutting processes and dust treatment technologies will continue to emerge, reducing the environmental impact of laser cutting. With continuous technological breakthroughs and the gradual reduction of costs, metal tube and pipe laser cutting machines will become more widespread, serving as the core force driving the high-quality development of the manufacturing industry and injecting a continuous stream of impetus into the global industrial progress.