In the grand landscape of modern manufacturing, laser welding machines shine like brilliant stars. With their exceptional performance and advanced technology, they have brought revolutionary changes to material joining processes. From high – end and precision electronic devices to automotive manufacturing that concerns travel safety, and then to the aerospace field that explores the mysteries of the universe, laser welding machines, with their unique “welding magic”, closely connect various materials and support the development of numerous industries. Today, let’s delve into the wonderful world of laser welding machines.
I. Working Principles of Laser Welding Machines
The core operation of a laser welding machine is to use a high – energy – density laser beam as a heat source to locally heat the materials. When the laser beam focuses on the material surface, its powerful energy is instantly absorbed by the material, causing the surface temperature to rise sharply, reaching the melting point or even the boiling point rapidly. As a result, the material melts or even vaporizes in a very short time.
Taking the welding of metal materials as an example, the energy radiated by the laser diffuses into the interior of the material through heat conduction, forming a specific molten pool inside the material. As the laser beam moves, the liquid metal in the molten pool cools and solidifies, firmly connecting the separated materials and completing the welding process. The entire process is like an “energy feast” in the microscopic world, where the laser beam precisely controls the release and transfer of energy to achieve the perfect fusion of materials.
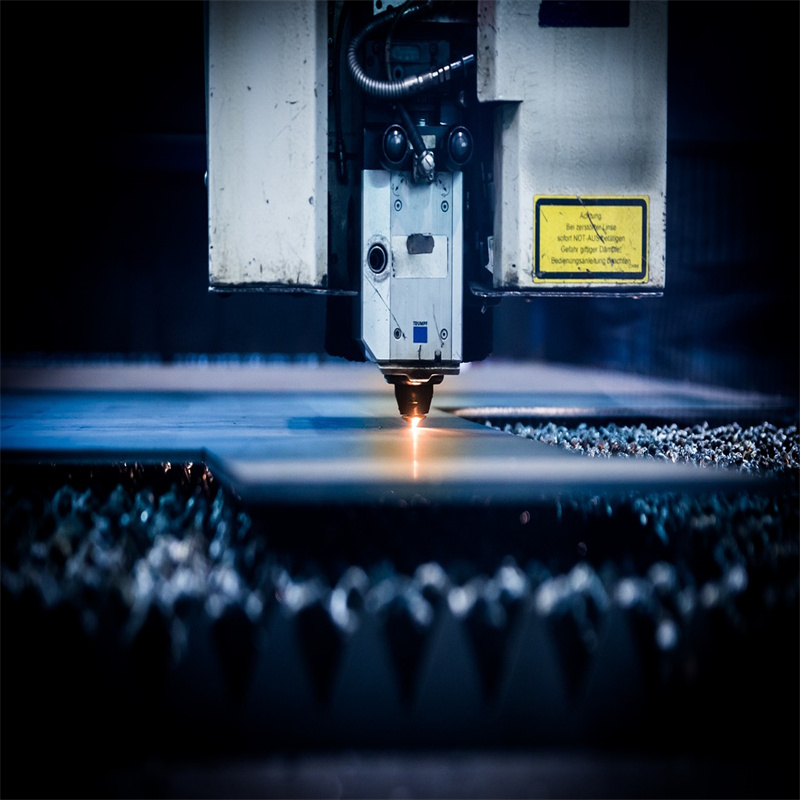
II. Types of Laser Welding Machines
(I) According to the Energy Output Mode of the Laser
- Pulse Laser Welding Machine: Just like precise “single shots”, the pulse laser welding machine outputs intermittent high – energy pulses. During the welding process, each pulse acts on the material surface, causing local melting of the material to form a solder joint. This method is especially suitable for spot welding of thin – sheet metal materials and the welding of materials sensitive to heat input. Due to the short pulse duration, the overall temperature rise of the workpiece is extremely small, the heat – affected zone is strictly limited to a very small area, and the degree of workpiece deformation is minimized. For example, in the welding of tiny metal components in electronic devices, the pulse laser welding machine can operate precisely, ensuring the welding quality without affecting the performance of surrounding components.
- Continuous Laser Welding Machine: Similar to a continuous “flow of water”, the continuous laser welding machine uses fiber lasers or semiconductor lasers as the core to continuously heat the workpiece surface. Its advantages are fully demonstrated when welding continuous welds. The laser beam continuously outputs energy, and the welding speed is extremely fast, which can greatly improve production efficiency. In scenarios such as the welding of vehicle body frames in automotive manufacturing, the continuous laser welding machine can efficiently complete the welding of long welds, ensuring the strength and stability of the body structure.
(II) According to the Power Density of the Laser Focused Spot
- Conduction – Mode Laser Welding Machine: When the conduction – mode laser welding machine works, the laser radiation mainly heats the surface of the workpiece, and the heat absorbed by the surface gradually diffuses into the interior of the material through heat conduction. By precisely controlling key parameters such as the waveform, width, peak power, and repetition frequency of the laser pulse, the surface temperature of the workpiece is raised to the melting point, forming a specific molten pool. This welding method is suitable for some welding tasks with low requirements for welding depth and good thermal conductivity of materials. For example, in the welding of some thin – plate metals, it can ensure a flat and beautiful weld surface.
- Deep Penetration Laser Welding Machine: The deep penetration laser welding machine generally uses a continuous laser beam for welding, and its metallurgical physical process is very similar to electron beam welding. The energy conversion is completed through a unique “keyhole effect”. Under the intense irradiation of a high – power – density laser, the material evaporates rapidly, forming a hole filled with vapor. This hole is like a “black body”, which can absorb almost all the incident light energy. The heat is transferred from the outer wall of the high – temperature hole cavity to the surroundings, melting the surrounding metal. Under the continuous irradiation of the laser beam, the surface tension of the liquid metal layer formed by the flow of the liquid metal outside the hole wall interacts with the continuously generated vapor pressure inside the hole cavity to maintain a dynamic balance. The deep penetration laser welding machine can achieve deep welding, with a high depth – to – width ratio of the weld. It is often used for welding thick metal materials, such as some key metal components in the aerospace field, ensuring that the welded joints have sufficient strength and reliability.
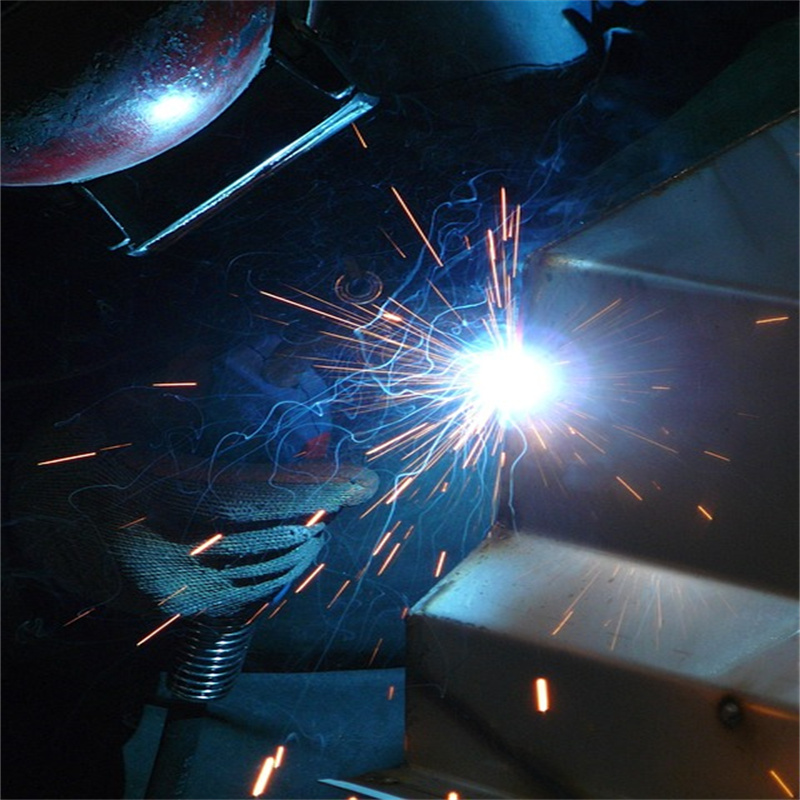
(III) According to the Type of Laser
- Fiber Laser Welding Machine: The fiber laser welding machine uses a fiber – transmitted laser, which has the significant advantage of high electro – optical conversion efficiency. It has a fast welding speed and can complete a large number of welding tasks in a short time. The equipped CCD camera monitoring system is like a “smart eye” for the welding machine, with precise positioning. Operators can observe the welding process in real – time, promptly detect and adjust problems. The characteristic of a small focused spot makes it good at micro – welding, capable of precisely welding materials or components with tiny sizes. Moreover, the fiber laser welding machine has no consumables, requires no maintenance, and has an extremely long service life, greatly reducing the use cost and maintenance workload. It is widely used in industries with extremely high requirements for welding accuracy and quality, such as precision 3C digital products, instruments and meters, and medical devices. For example, in the welding of mobile phone camera modules, it can complete the welding of tiny solder joints with high precision, ensuring the stable performance of the camera.
- CO₂ Laser Welding Machine: The CO₂ laser welding machine has a strong output power, especially suitable for welding thick materials with high requirements for heat input. The laser it generates has a relatively long wavelength, which can be better absorbed by some materials during the welding process, enabling efficient welding. In the welding of some large – scale metal structural parts, such as the welding of thick steel plates in shipbuilding, the CO₂ laser welding machine can penetrate deep into the material with its powerful power, forming a firm weld and ensuring the strength and safety of the structural parts.
- Disk Laser Welding Machine: The disk laser welding machine excels in high power and high beam quality. The high power ensures that there is sufficient energy to quickly melt the materials during the welding process, while the high beam quality makes the energy distribution of the laser beam more uniform and concentrated during propagation, enabling more precise welding. In industrial production scenarios with extremely strict requirements for welding quality, such as the welding of precision components in high – end electronic devices and the manufacturing of key components like aero – engine blades, the disk laser welding machine plays an important role and can meet the extremely high requirements of these industries for welding accuracy, strength, and reliability.
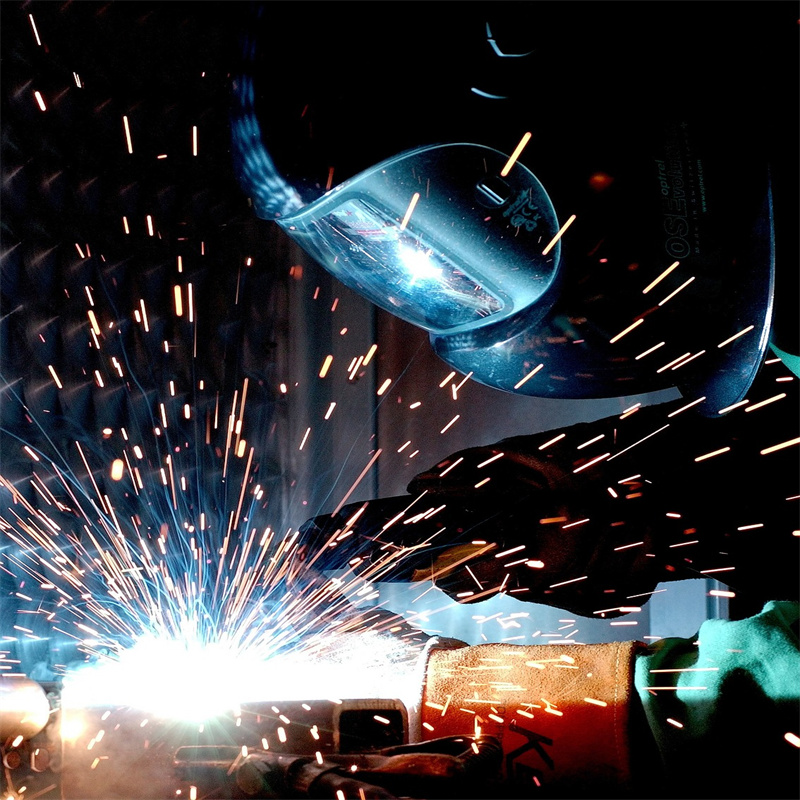
V. Looking to the Future
With the continuous progress of science and technology, laser welding machine technology is also constantly innovating and developing. In the future, laser welding machines will move towards higher power, higher precision, and greater intelligence. On the one hand, laser welding machines with higher power will be able to weld thicker and more refractory materials, expanding their application fields; on the other hand, by introducing advanced sensor technology and intelligent control systems, laser welding machines will achieve more precise control of the welding process. They will be able to adjust welding parameters in real – time according to material properties and welding requirements, further improving welding quality and efficiency. In addition, with the increasing popularity of the concept of green manufacturing, laser welding machines will also be continuously optimized in terms of energy conservation, consumption reduction, and environmental pollution reduction, contributing more to the sustainable development of the manufacturing industry. It is believed that in the future, laser welding machines will show their unique charm in more fields and play an even more important role in promoting industrial progress and social development.